Disconnected Systems: The Silent Barrier to Supply Chain Performance
Dec 4, 2024 11:52:11 AM - 6 min read
.png)
PlaniSense
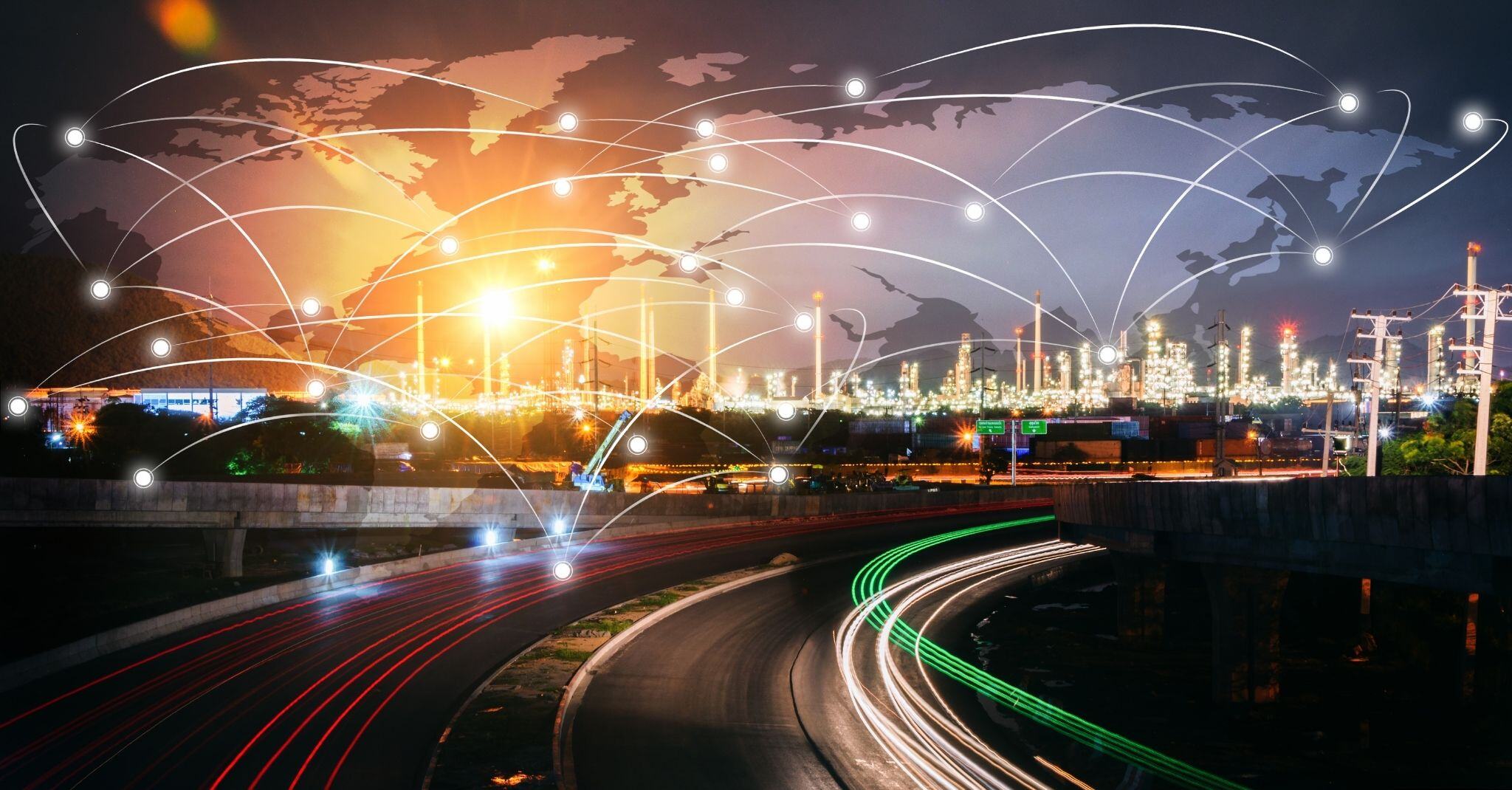
In the Supply Chain sector, digital transformation is progressing rapidly, driven by the growing need for agility and seamless communication between systems. Companies are increasingly adopting specialized software solutions to optimize every aspect of their chain, from inventory management to production planning. However, the lack of integration between these tools creates data silos, which poses a major challenge to operational efficiency. Without connectivity between systems, critical processes can be slowed down, leading to costly errors, wasted time, and ultimately, a negative impact on the company’s overall performance.
Context
Digitalization
Digitalization is redefining how the Supply Chain operates within companies, pushing them to adopt a variety of specialized software solutions to meet the demands for precision, speed, and flexibility. Each domain—be it logistics, inventory management, production, or planning—now relies on advanced tools tailored to the needs of individual departments. However, this proliferation of fragmented solutions often leads to data silos. Crucial information, generated and stored in separate systems, remains isolated and difficult to synchronize, complicating information sharing and real-time tracking.
The lack of communication between these systems results in redundant data entry and human errors, which burden processes and slow down decision-making. By limiting agility and overall efficiency, this data segmentation can undermine a company's performance and hinder its ability to adapt to an ever-changing market. Instead of enhancing their responsiveness, companies risk losing their competitive edge due to disconnected processes and a fragmented view of their Supply Chain.
Need for Agility
Modern Supply Chains face rapidly changing cycles where agility and adaptability are crucial. Whether responding to fluctuations in demand, supplier disruptions, or logistical constraints, companies must be able to adjust their operations without delay. This requires real-time visibility across all activities and seamless information flow between various systems. Unfortunately, the lack of communication between specialized software limits this visibility and hampers responsiveness, forcing teams to make decisions based on incomplete or outdated information.
Potential consequences
The disconnect between software systems used in the Supply Chain results in numerous tangible consequences that hinder operational efficiency and customer satisfaction. The lack of integration forces teams to perform redundant data entries, significantly increasing the risk of input errors. For instance, when an employee manually enters stock or production information across multiple systems, even a minor inconsistency or typo can compromise data integrity throughout the entire chain. These errors can cascade, leading to discrepancies in supply data, customer orders, and production planning, thereby complicating flow management.
Not only do these repeated entries increase the workload for teams, but they also consume valuable resources that could be redirected toward more strategic tasks. Instead of focusing on high-value activities like process optimization or improving responsiveness, teams must spend time correcting errors and manually syncing information across systems. These inefficiencies introduce additional delays in operations, directly impacting on a company’s ability to respond swiftly to demand fluctuations or urgent customer needs. Ultimately, customers may become dissatisfied with longer processing times or errors in order management, which can harm the company’s reputation and its long-term relationships with business partners.
What Are the Challenges for Your Supply Chain and Operational Excellence?
Supply Chain Departments Affected by Redundant Data Entry
In the Supply Chain, several departments are particularly affected by redundant data entry. Procurement, for instance, relies on accurate and up-to-date information to manage orders and anticipate raw material needs. When this data must be re-entered manually, the risk of errors increases, potentially leading to stock shortages or overages.
The production planning department also feels the direct impact of such redundancies. Incorrect or outdated data skews schedules, adjusting more challenging. These repeated manual entries waste valuable time and lead to frustration and dissatisfaction among teams, who struggle to optimize processes under these constraints.
In scheduling (short-term operations management), even minor data entry errors can have significant repercussions on operational consistency. For example, a simple typo in the production quantity can create a mismatch between actual production capacity and identified needs. This often results in imbalanced manufacturing: some products are overproduced, leading to unnecessary inventory, while others—sometimes critical—are underproduced or unavailable. These discrepancies not only disrupt production flows but also negatively impact customer satisfaction (e.g., stockouts, missed delivery deadlines) and force teams to implement costly, time-consuming adjustments.
Why This Issue Is More Prevalent Today Than It Was 10 Years Ago
Today's businesses rely on an ever-increasing number of specialized tools and software to manage the various facets of their Supply Chain, which has become more complex and comprehensive than in the past. While this diversity of tools enables precise management of specific functions—whether logistics, inventory, or production planning—it also introduces challenges in data handling. The more systems there are, the greater the need for fast and seamless synchronization of information to ensure optimal responsiveness.
In this context, reaction times must be extremely short for companies to adapt effectively to demand fluctuations or logistical disruptions. Without smooth and rapid data flow between systems, teams are forced to rely on outdated or incomplete information, significantly limiting their ability to make informed and agile decisions.
Elements of the Supply Chain Affected by Lack of Connectivity
The lack of connectivity between systems is particularly impactful in several key areas of the Supply Chain, where manual data entry becomes a recurring task. For instance, planning systems often require teams to re-enter information, increasing the risk of errors in quantities or locations. Similarly, in order execution, the absence of seamless communication between order management software and logistics systems can lead to update delays. This forces operators to manually input tracking data, complicating processes and heightening the risk of discrepancies.
Clients frequently highlight the challenges this lack of connectivity creates in daily operations: not only do teams lose valuable time managing redundant tasks, but they are also exposed to errors that can affect the speed and quality of operations. This constant need for manual entry creates a significant workload, reducing team efficiency and disrupting the overall fluidity of the Supply Chain.
How PlaniSense Integrates a Solution
Connection to ERP and IT Environment
PlaniSense stands out for its ability to seamlessly integrate with ERPs, eliminating the need for repetitive manual data entry, as well as with other key IT systems such as MES (Manufacturing Execution System) and WMS (Warehouse Management System). By enabling these connections, PlaniSense ensures a smooth flow of data across various software platforms. This integration centralizes and synchronizes critical information in real time, reducing error risks and providing complete visibility over all operations. Teams can rely on continuously updated and easily accessible data, enhancing both the accuracy and speed of daily decision-making.
Plan Modification Features for Enhanced Agility
PlaniSense's plan review and modification features provide unprecedented agility in the face of demand fluctuations or logistical disruptions. With intuitive and powerful rescheduling tools, teams can quickly adjust forecasts and production plans based on the latest available data. Whether responding to a sudden surge in orders or adapting operations to supply chain disruptions, PlaniSense enables optimal responsiveness. Companies can minimize delays while optimizing inventory management, strengthening their ability to adapt to market changes efficiently.
User Access and Data Security
PlaniSense offers role-based access control to efficiently manage user permissions according to their level of authorization. Each user can access the information relevant to their role, either in editing or view-only mode, depending on their rights, while benefiting from secure and up-to-date data. This rights management system not only protects the confidentiality of sensitive information but also promotes seamless collaboration across different departments. By ensuring all teams work with the same updated data, PlaniSense enhances operational consistency and reduces the risks of mishandling or spreading inaccurate information.
Additional Benefits: Improved Communication Between Departments
Beyond its technical features, PlaniSense also fosters better communication among departments such as planning, production, and logistics. By centralizing information and making it accessible to all relevant teams, PlaniSense facilitates exchanges and coordination, leading to smoother processes and improved synchronization across operations. This transparency reduces the risk of misunderstandings or conflicts between departments, enabling a more harmonious execution of the Supply Chain and an overall improvement in organizational efficiency.
Conclusion
The lack of communication between different Supply Chain systems creates significant challenges: data entry errors, redundant tasks, and delays that hinder operational efficiency and responsiveness. Without seamless connectivity between software platforms, information flow becomes fragmented, complicating decision-making and reducing agility in the face of demand fluctuations.
Planning systems like PlaniSense address these challenges by delivering substantial benefits: increased efficiency through automated data flows, improved accuracy that minimizes human errors, and enhanced agility for quick adjustments to unforeseen events. By strengthening Supply Chain resilience, PlaniSense frees businesses from operational constraints, enabling them to focus on strategic initiatives that drive growth and bolster competitiveness in the market.