6 erreurs à éviter pour maximiser le TRS et optimiser la production
Dec 17, 2024 4:39:47 PM - 5 min read
Romain
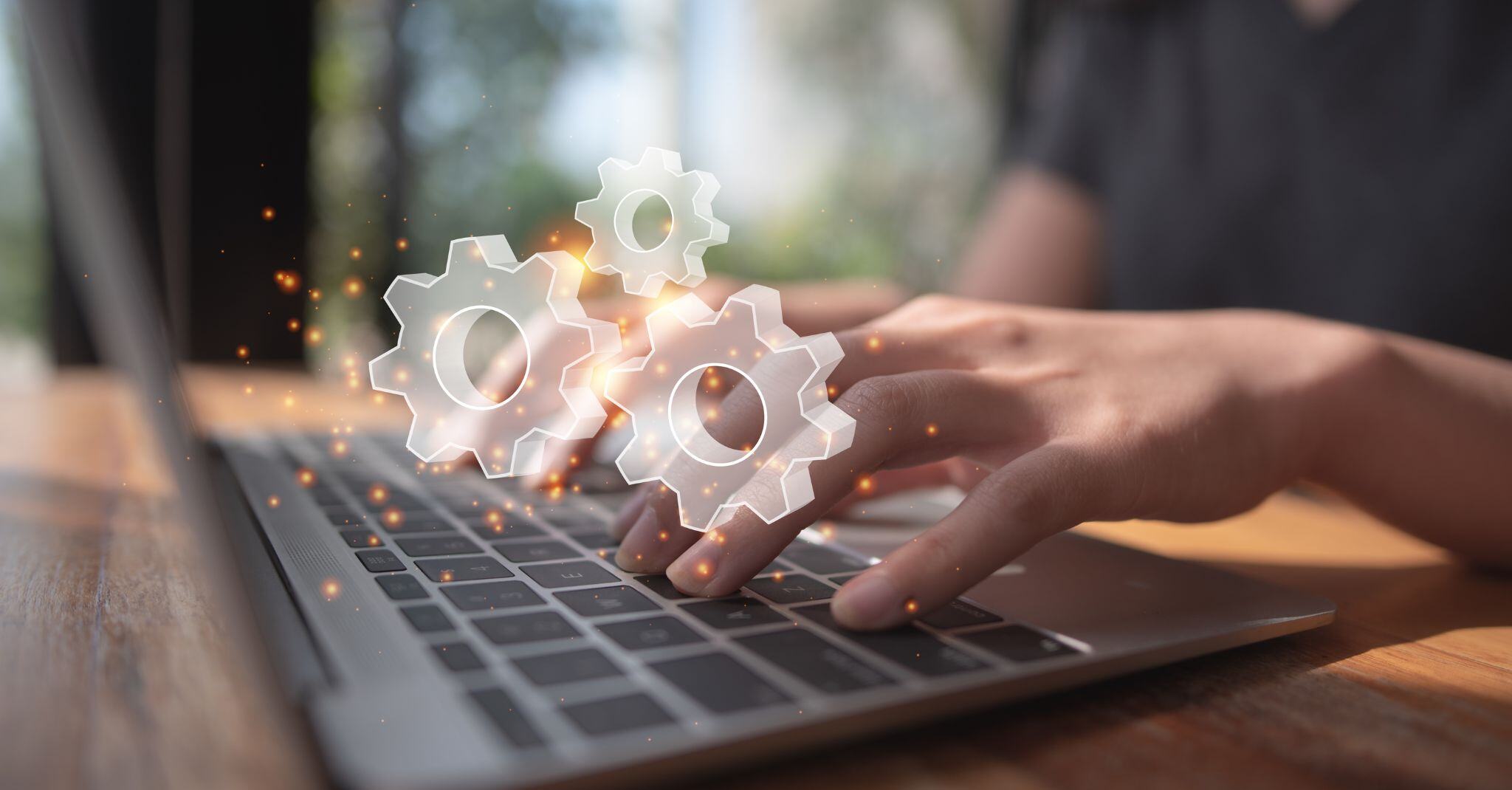
Dans le monde de l’industrie, tirer le meilleur parti de ses équipements n’est plus une option mais une nécessité. Une machine qui tourne en sous-régime ou qui n’est pas exploitée à son plein potentiel peut vite peser lourd dans les résultats financiers. Pour garder le cap et améliorer les performances, les entreprises s’appuient sur un indicateur incontournable : l’efficacité globale des équipements, ou OEE (Overall Equipment Effectiveness).
Le TRS (Taux de rendement Synthétique) se concentre sur trois dimensions essentielles de la production : la disponibilité, la qualité et la performance. Bien maîtrisé, il devient un véritable levier pour identifier les points d’amélioration et optimiser les processus. Mais attention, des erreurs fréquentes peuvent limiter son impact.
Dans cet article, nous allons explorer les erreurs les plus fréquentes liées au TRS (Taux de rendement Synthétique) et voir comment PlaniSense peut vous accompagner afin de les éviter.
Compréhension du Taux de rendement synthétique
Le TRS (Taux de rendement Synthétique) est un indicateur clé dans la gestion d’une industrie, il est suivi de très près par la plupart des dirigeant et est une valeur incontournable dans les résultats financier.
Le TRS ou OEE dans sa traduction anglophone mesure la divergence entre la production réelle et la production théorique. Améliorer le TRS c’est donc trouver des solutions pour augmenter la production réelle et la rapprocher de la production théorique qui elle est figée car elle dépend des caractéristiques techniques des machines et des outils.
1. Comparer les taux de rendement Synthétique entre différents sites ou processus
L’un des grands avantages du TRS (Taux de rendement Synthétique) est qu’il synthétise les performances d’une machine ou d’un processus en un chiffre unique. Mais cette simplicité peut vite devenir un piège. On a tendance à vouloir comparer ce chiffre d’un site à l’autre ou entre différents systèmes de production, sans vraiment prendre en compte les différences : type de machine, produit fabriqué, ou encore contexte opérationnel.
Ces comparaisons, souvent biaisées, mènent à des conclusions erronées. En réalité, le TRS est bien plus utile lorsqu’on l’utilise pour suivre l’évolution d’une machine ou d’une ligne de production dans le temps. C’est en observant les tendances que l’on peut repérer les variations, comprendre ce qui fonctionne (ou non) et ajuster les processus en conséquence.
Avec PlaniSense, nos outils d’analyse sont conçus pour se concentrer sur les évolutions internes plutôt que sur des comparaisons générales, garantissant une interprétation des données pertinentes et ciblées pour guider vos décisions.
2. Zoomer pour gagner : pourquoi l’analyse détaillée du TRS est essentielle
Regrouper les TRS de plusieurs machines pour obtenir une moyenne globale peut sembler utile pour obtenir une vue d’ensemble. Pourtant, cette approche risque de cacher des problèmes spécifiques à certaines machines ou lignes de production. En clair, une moyenne globale ne vous dira jamais où se situent précisément les problèmes ni quelles sont vos plus grandes opportunités d’amélioration.
La clé d’une amélioration efficace réside dans une analyse détaillée. En commençant par chaque machine individuellement, il devient possible de diagnostiquer les sources de perte, d’élaborer des plans d’action spécifiques, puis de généraliser ces bonnes pratiques à l’ensemble des équipements.
3. Analyser sur des périodes trop courtes
Pour que les données TRS soient exploitables, elles doivent être collectées sur des périodes significatives. Se concentrer uniquement sur une journée ou un quart de travail, risque de faire manquer l’essentiel. Les analyses basées sur des journées isolées ou des quarts de travail sont souvent biaisées : elles manquent de données et exagèrent l’impact d’événements ponctuels, comme un arrêt imprévu.
Un horizon plus long, comme une semaine ou un mois, permet de lisser les variations et d’obtenir une vue d’ensemble bien plus fiable. Cela donne une vision plus réaliste des performances et aide à prioriser les actions correctives.
PlaniSense propose des outils de suivi flexibles permettant de centrer l’analyse à des périodes adaptés à la réalité de chaque client, garantissant des données fiables et significatives.
4. Négliger l’implication des équipes terrain
Les opérateurs et techniciens sont au cœur des processus de production. Ils connaissent leurs machines mieux que quiconque et peuvent fournir des informations précieuses sur les causes des inefficacités. Les exclure du processus d’analyse ou de mise en œuvre des mesures correctives est une erreur fréquente qui limite l’efficacité des initiatives d’amélioration.
En impliquant les équipes dès le départ et en favorisant une communication ouverte, il est possible de développer des solutions qui collent aux besoins du terrain et de renforcer l’engagement des employés dans l’amélioration continue.
5. Se concentrer uniquement sur le TRS
Le TRS donne une vue d’ensemble claire des performances et met en lumière les pertes, mais ne révèle pas forcément les causes. Trop souvent, les entreprises se focalisent uniquement sur le chiffre global sans chercher à comprendre les dysfonctionnements sous-jacents.
Le TRS doit être vu comme un point de départ. Une analyse approfondie est nécessaire pour identifier les causes des pertes de disponibilité, de qualité ou de performance.
6. Collecter les données manuellement
Aujourd’hui, avec l’automatisation et la digitalisation qui révolutionnent l’industrie, la collecte manuelle des données TRS est devenue obsolète. Non seulement elle demande beaucoup de temps, mais elle ouvre la porte aux erreurs humaines, ce qui rendra les résultats peu fiables.
L’automatisation permet d’obtenir des données précises en temps réel, sans risque de biais ou d’oubli. Cela libère du temps aux opérateurs afin qu’ils puissent se concentrer sur la résolution des problèmes qui pénalisent le TRS des machines ou des processus.
Conclusion
Le TRS est un outil essentiel pour mesurer les performances des systèmes de production. Cependant, son efficacité dépend de la manière dont il est utilisé. Comparaisons inappropriées, analyses sur des périodes trop courtes, collecte manuelle des données... Ces erreurs peuvent limiter son potentiel.
Avec PlaniSense, les entreprises disposent d’une solution complète qui leur permet de surmonter ces obstacles et d’améliorer leurs TRS. Grâce à des analyses précises, des visualisations adaptées et une collaboration renforcée entre les équipes, nous aidons nos clients à atteindre des niveaux inédits d’efficacité et de performance.
Prêt à transformer votre production grâce à une approche avancée du TRS ?
Contactez PlaniSense dès aujourd’hui pour une démonstration de nos solutions et découvrez comment nous pouvons vous aider à améliorer vos performances, réduire vos coûts et atteindre vos objectifs stratégiques.