PlaniSense is designed to be extremely flexible and adaptable, enabling it to respond effectively to the production planning and management needs of a wide range of industrial sectors. Thanks to its modular architecture and customization capabilities, PlaniSense can be configured to meet the specific operational, production and regulatory requirements of each industry, whether automotive, pharmaceutical, electronics or consumer goods.
A New Chapter in Production Planning at Bel Group
May 3, 2024 11:08:34 AM - 6 min read
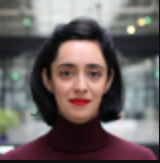
Ana Sofia
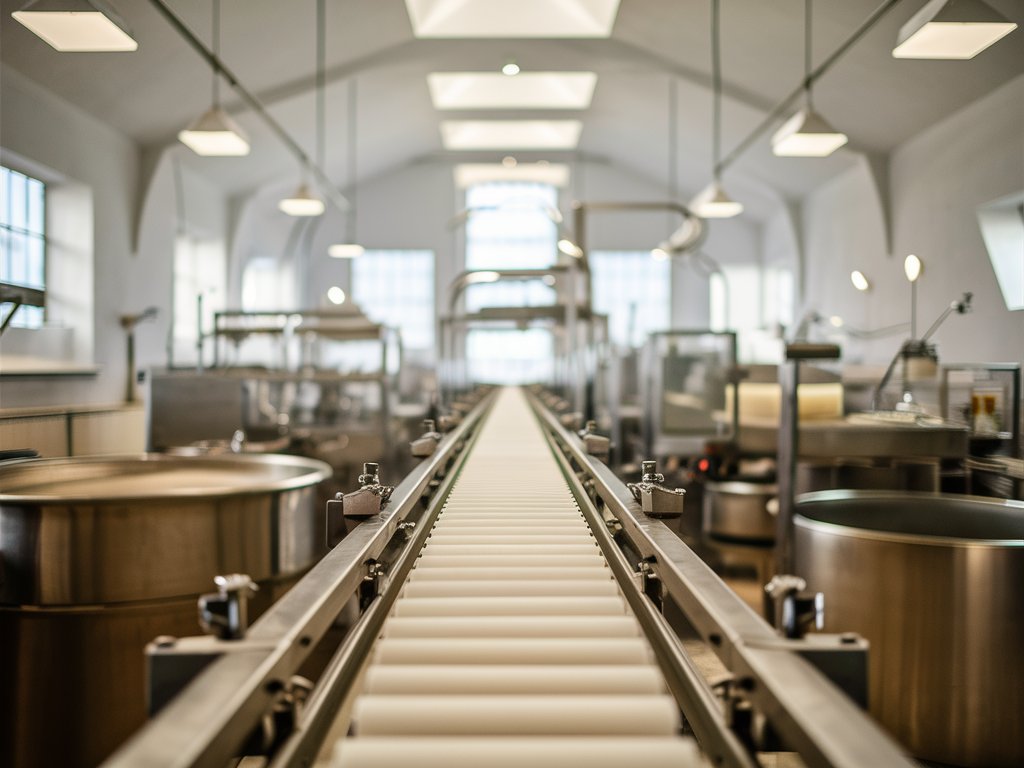
Today's industry is marked by the increasing complexity of in-house production processes, while facing growing uncertainty about downstream demand and the availability of upstream materials and components. Bel Group, a major player in the food industry known for its iconic brands such as The Laughing Cow, Babybel and Kiri, is no exception to this reality. Faced with the challenge of optimizing the use of its resources in a context of great uncertainty, the group has undertaken a major strategic shift by integrating the PlaniSense solution at the heart of its operational planning process.
The transformation brought about by the introduction of an Advanced Planning System (APS) represents a significant step forward in the deployment of the group's industrial strategy. This article explores the context of this transformation, the challenges encountered, and the solutions provided by PlaniSense in the emblematic case of the Lons-le-Saunier plant.
The Situation Before PlaniSense
Historically, the Lons-le-Saunier plant, Bel Group's production pillar, faced many production planning challenges. The growing diversity of products, the demand for customization by market, and complex industrial constraints formed a daily headache for planners and schedulers. Managing this complexity using outdated tools, mainly Excel spreadsheets, only exacerbated the difficulties encountered, resulting in considerable loss of time, reduced reliability of production plans, and high risks of error.
The Shift with PlaniSense
Bel Group's decision to adopt PlaniSense was motivated by the need to respond effectively to these challenges. PlaniSense stood out as an innovative Supply Planning solution, capable of seamless integration with existing systems (notably SAP), while offering the flexibility needed to adapt to the specificities of each plant and production line. The deployment project, although launched in an unprecedented context of confinement, followed an agile approach, enabling efficient implementation and continuous adaptation to user needs.
The benefits of a new solution
The introduction of PlaniSense has brought about a significant transformation at the Lons-le-Saunier plant, with positive impacts on several levels:
- Optimization of time and resources: Reducing the time spent on scheduling and planning freed up valuable resources, which were reallocated to value-added tasks. Automatic entry of production orders eliminated manual entry errors, reinforcing the reliability of the production tracking process.
- Improved responsiveness and flexibility: Faced with frequent changes to production plans, PlaniSense offered unrivalled agility, enabling rapid and precise adjustments. Increased real-time inventory visibility facilitated better resource management and a reduction in obsolete stock, crucial for efficient production line management.
- Enhanced standardization and collaboration: The solution has harmonized planning practices across the Group's various plants, while facilitating information sharing and collaboration between teams. This has enabled a better understanding and anticipation of production needs, consolidating operational efficiency and reinforcing the Group's global industrial plan.
Towards a Promising Future
Bel Group's experience with PlaniSense opens the way to new perspectives, not only in terms of optimizing planning and production, but also in the way we approach innovation and digital transformation in the food industry. The lessons learned from this project demonstrate the crucial importance of adaptability, technological integration, and user involvement in the success of such an initiative.
Conclusion
The collaboration between Bel Group and PlaniSense is an eloquent example of how technology can transform industrial operations, providing concrete solutions to the challenges of production planning and management. This transformation, beyond the operational improvements it generates, reflects a paradigm shift in industry, where flexibility, responsiveness and optimization are becoming the watchwords.
The success of the PlaniSense project also underlines the importance, for a large group like BEL, of choosing technology partners who are aware of the industry's specific challenges and capable of offering scalable solutions. It also underlines the crucial role of in-house teams in the transformation process throughout the project lifecycle.
The Bel Group plans to extend the use of PlaniSense to other aspects of its operations, exploring new ways to improve efficiency, reduce costs and meet customer expectations even more effectively.
FAQ
PlaniSense uses advanced optimization algorithms and finite-capacity planning technologies to effectively manage the complexity inherent in modern production systems. It considers many variables and constraints, such as production lead times, machine capacities, human resources, changeover times, and storage and logistics constraints. By carrying out an in-depth analysis of these factors, PlaniSense proposes optimized production plans that maximize efficiency while minimizing costs and lead times.
Integrating PlaniSense with an ERP system such as SAP brings several significant advantages. It ensures that production, inventory, order and resource information is synchronized and consistent across the entire information system. This integration makes planning more accurate and responsive, improves visibility across all operations, and supports informed decision-making. What is more, it helps to reduce double entries and the associated risk of errors.