The integration of PlaniSense has enabled Guerlain to significantly improve the efficiency of its production processes. This results in a noticeable reduction in costs through better use of resources and more accurate planning.
Guerlain: Towards a more efficient production planning
Sep 30, 2024 4:08:11 PM - 5 min read
Nursultan
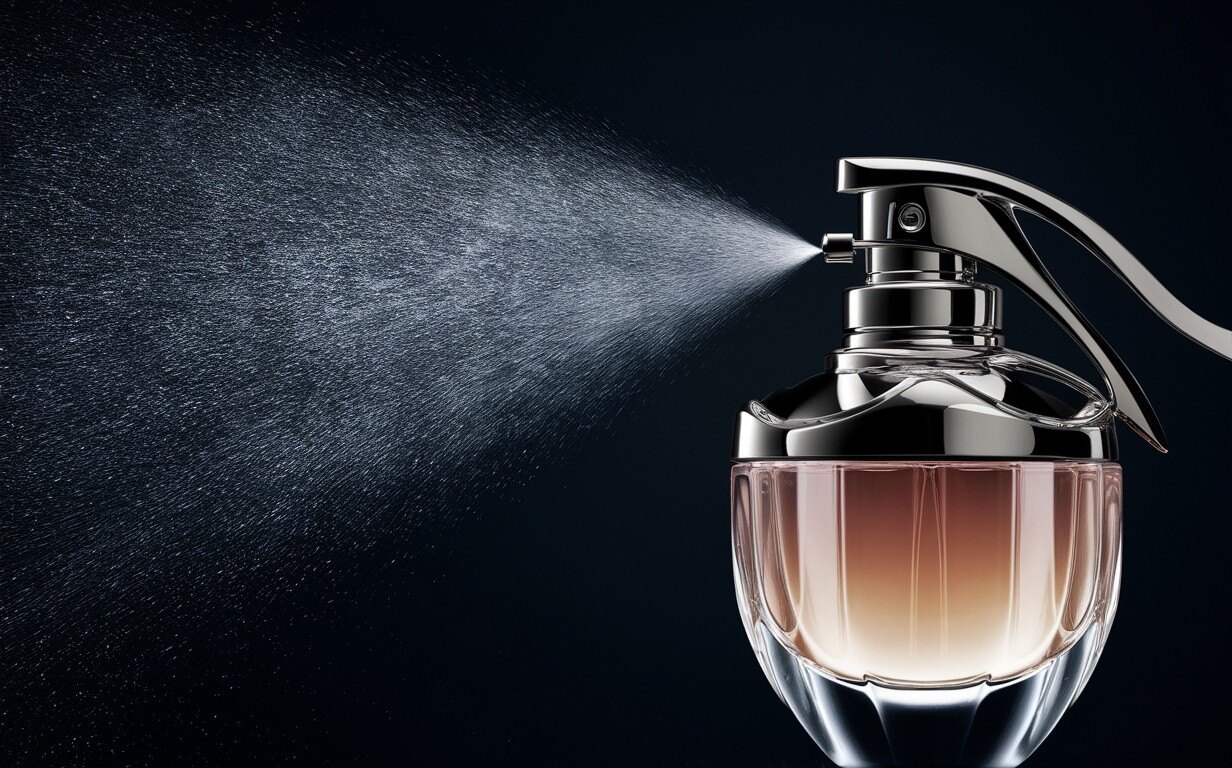
Guerlain, a prestigious luxury brand, has radically changed its planning practices by adopting PlaniSense, a modern solution equipped with advanced simulation and optimization features.
This article examines how the PlaniSense solution was implemented at Guerlain through a description of the initial state, the implementation steps and the gains obtained.
Situation before PlaniSense
Prior to adopting PlaniSense, Guerlain's teams relied exclusively on SAP for short and mid-term planning of downstream packaging lines and upstream manufacturing workshops. While robust, SAP has flexibility gaps, especially when it comes to quickly adjusting production in response to fluctuations in demand and/or operational hazards in a context of limited capacity. To compensate for this rigidity, Guerlain had to make costly investments to increase the limiting production capacities (maceration and storage tanks in the manufacturing workshops).
This situation clearly highlighted the need for Guerlain to implement a more dynamic planning solution integrated with SAP. The transition to a solution like PlaniSense was seen as a key factor that would enable Guerlain to optimize resource utilization and streamline investments in storage and production capacities.
Implementation
The deployment of PlaniSense at Guerlain was carefully planned to ensure a seamless integration with existing systems, particularly SAP. The project began with a series of workshops aimed at assessing PlaniSense's compatibility with Guerlain's specific processes and identifying the necessary adjustments.
This phase proved essential not only to ensure that PlaniSense met Guerlain’s needs but also to allow operational teams to become familiar with the new simulation and decision-support features that would enhance their daily work. After observing promising results and tangible improvements within a limited scope, Guerlain approved the implementation of the PlaniSense solution using an Agile project approach.
The deployment strategy was designed to gradually integrate PlaniSense with minimal disruption to daily operations. PlaniSense's interoperability with SAP played a crucial role by ensuring real-time data consistency and synchronization across the various components of the information system.
The gradual implementation using the Agile methodology greatly facilitated the adoption of PlaniSense by Guerlain’s teams, who quickly gained access to an initial version of the solution. This version was then progressively enhanced, thanks to the active involvement of end users.
Benefits
PlaniSense has led to substantial operational improvements. First, the increased flexibility in planning allowed Guerlain to quickly adapt to demand fluctuations and operational uncertainties. This enhanced flexibility reduced production lead times, thereby improving the company’s ability to promptly meet market demands.
PlaniSense also introduced advanced visualization and simulation tools that enabled more efficient management of inventories and limiting resources (such as storage and maceration tanks). These features allowed Guerlain to minimize excess stock while optimizing equipment utilization. As a result, the company significantly reduced production costs and streamlined its capacity investments.
Moreover, PlaniSense enhanced interdepartmental collaboration. By providing up-to-date and consistent data, the solution facilitated better coordination among the various internal stakeholders involved in the planning process. Improved communication greatly contributed to aligning operational activities with the company’s strategic objectives.
Finally, risk management at Guerlain was strengthened through PlaniSense’s predictive capabilities, which helped better anticipate and manage unforeseen events in the tank operations.
In summary, the integration of PlaniSense at Guerlain marked a significant step forward in how the company approaches production planning in its perfume manufacturing workshop, highlighting the importance of adopting cutting-edge technological solutions to remain competitive in a constantly evolving global market.
Return on investment
The deployment of PlaniSense at Guerlain has resulted in a significant and almost immediate return on investment, which is manifested through multiple aspects of the project, including the three essential points described below.
-
The company was planning to launch a large, expensive expansion project to increase its storage and maceration capacity (purchase of additional tanks and infrastructure works). The optimization of resources carried out with PlaniSense made it possible to identify viable production scenarios in the medium and long term within the limits of existing capacities. Several million euros of investment have thus been saved.
-
More precisely, PlaniSense has made it possible to reduce the saturation rate by around 20% with the existing tanks. This optimization directly increased production capacity and made the physical expansion project of the facility unnecessary.
-
With better visibility and advanced simulation capabilities, the company has been able to establish more efficient production plans that help improve team productivity, improve service levels and keep inventory levels under control.
Conclusion
The integration of PlaniSense at Guerlain is a perfect example of how a planning solution based on modern technologies can radically transform existing practices. By adopting a flexible and integrated solution, Guerlain has not only improved the efficiency of its production processes, but has also redefined its processes and standards to better take into account the operational complexity specific to the luxury industry.
FAQ
PlaniSense is equipped with advanced visualization and simulation features that have enabled more efficient management of inventory and production resources. This helped the company quickly adjust its production capabilities based on market fluctuations and operational hazards.
PlaniSense helps to overcome several major challenges such as adapting to fluctuations in demand, inventory management and the use of human and material resources. PlaniSense also helps improve cross-departmental collaboration and risk management.
By enabling more efficient management of production resources, Guerlain's adoption of PlaniSense has significantly reduced operational costs and avoided unnecessary capital expenditures.