End-to-End Supply Chain Planning: Challenges and Solutions
Sep 20, 2024 4:11:07 PM - 5 min read
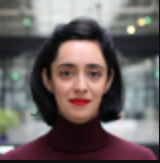
Ana Sofia
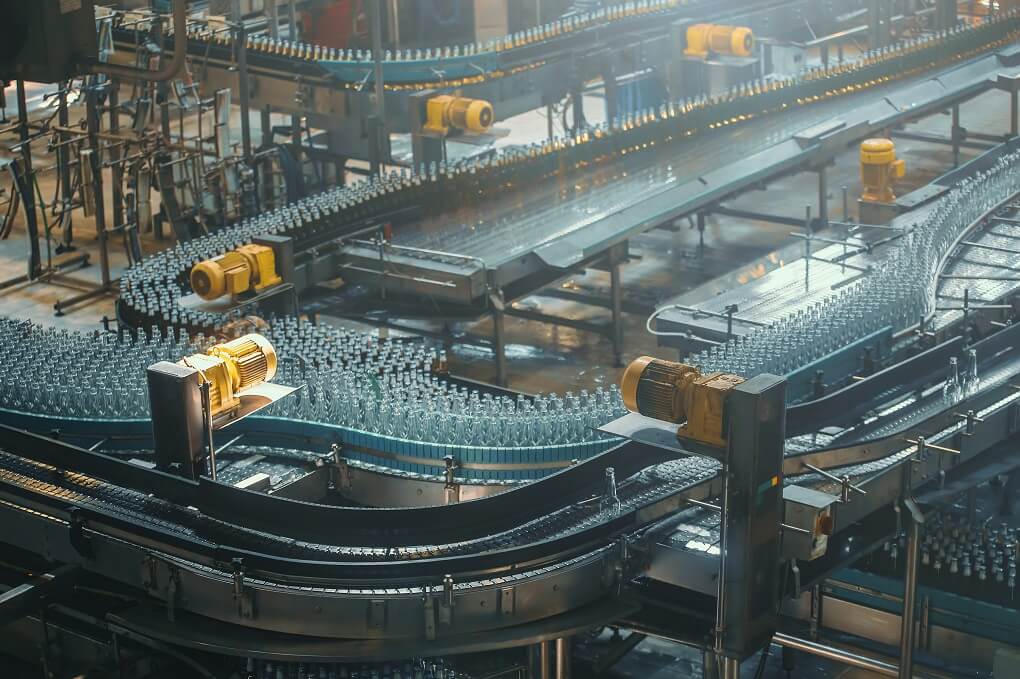
Integrating every aspect of the Supply Chain—from sourcing raw materials to delivering finished products—into a cohesive plan is one of the most complex tasks in modern business. This integration is particularly challenging in the production phase, where the transformation of raw materials into finished goods must be carefully coordinated with both upstream and downstream activities.
Understanding the Complexities of End-to-End Supply Chain Planning
End-to-End Supply Chain Planning requires viewing and managing the Supply Chain as a unified system rather than as isolated components. The goal is to ensure that each phase—sourcing, production, inventory management, distribution, and delivery—operates in harmony with the others. However, achieving such integration is no small feat.
The complexity arises from the need to synchronize numerous variables across different stages of the Supply Chain. Each segment has its unique dynamics and disruptions in one area can easily cascade through the entire chain. For example, delays in sourcing materials can lead to production bottlenecks, missed deadlines, and ultimately, customer dissatisfaction. The production phase, where raw materials are converted into finished goods, is particularly vulnerable to these disruptions.
Production planning must account for a wide range of factors, including machine availability, labor skills, quality control, and capacity constraints. All these elements need to be in sync with upstream supply activities and downstream delivery schedules. Additionally, the growing demand for customized products and faster turnaround times adds another layer of complexity, making agile and responsive production planning more critical than ever.
Key Challenges in Production Planning
Within an End-to-End Supply Chain, production planning presents several key challenges. One of the most significant is achieving the right balance between supply and demand. Production schedules must be finely tuned to meet customer demand without leading to overproduction, which can result in excess inventory and higher holding costs. On the flip side, underproduction can cause stockouts, lost sales, and strained customer relationships.
Managing production schedules in the face of uncertainties is another major challenge. Supply Chain disruptions—such as sudden changes in demand, supplier delays, or unexpected equipment failures—can throw production plans off course. Companies lacking in adaptive planning capabilities often find themselves with inefficiencies and increased operational costs when disruptions occur.
Effective Solutions for Production Planning
To address the challenges of production planning within an End-to-End Supply Chain, companies must employ a combination of strategic and operational planning. The following solutions, supported by industry best practices, offer a roadmap for creating a more cohesive and resilient production plan.
Implement Integrated Planning Systems
Integrated planning systems are crucial for managing the complexities of production planning. These platforms offer a unified view of all Supply Chain elements, enabling real-time data sharing and collaboration across departments. Such systems help align production schedules with both supply and demand, thereby reducing lead times, minimizing inventory costs, and enhancing overall Supply Chain responsiveness. Companies that have adopted integrated planning systems have reported operational efficiency improvements of up to 60%.
Leverage Advanced Analytics and Forecasting
Advanced analytics and forecasting tools are essential for navigating the uncertainties in production planning. By leveraging predictive analytics, companies can anticipate shifts in demand and adjust production schedules proactively. This data-driven approach leads to more accurate forecasts and optimized production plans. Organizations that effectively use data analytics for demand forecasting see improved order fill rates and reduced instances of stockouts, making it a vital tool in the planner’s toolkit.
Adopt Agile Manufacturing Practices
Agility in manufacturing is becoming increasingly important as the demand for customization and shorter product life cycles grows. Agile manufacturing practices emphasize flexibility and rapid adaptation to changes in customer requirements or market conditions. This often involves modular production systems that can be reconfigured quickly to accommodate different products or variations. Companies that have implemented agile manufacturing practices have seen up to a 20% improvement in time-to-market, critical in today’s competitive landscape.
Foster Collaborative Supply Chain Networks
Collaboration across the Supply Chain is another key element of effective production planning. Building strong partnerships with suppliers, distributors, and other stakeholders ensures better synchronization of activities and more efficient resource utilization. Practices such as Collaborative Planning, Forecasting, and Replenishment (CPFR) allow companies to share information and coordinate efforts, enhancing visibility across the Supply Chain and reducing risks. Companies with highly collaborative networks have achieved inventory holding cost reductions of up to 25%.
Conclusion
End-to-End Supply Chain Planning is a complex yet essential process for organizations aiming to maintain a competitive edge in today’s rapidly changing market. Production, as a central component of the Supply Chain, presents unique challenges that require a combination of strategic foresight, advanced technologies, and strong collaboration to overcome. By implementing integrated planning systems, leveraging advanced analytics, adopting agile manufacturing practices, fostering collaborative networks, and embracing continuous improvement, companies can create a resilient production plan that seamlessly integrates with the broader Supply Chain.
Addressing production planning challenges with innovative solutions and a commitment to continuous improvement allows companies not only to meet current demands but also to position themselves for future success in an increasingly interconnected world.